- Home
- Company
- Newsroom
- Hilti Stories
- Tackling the Global Housing Crisis With Bamboo
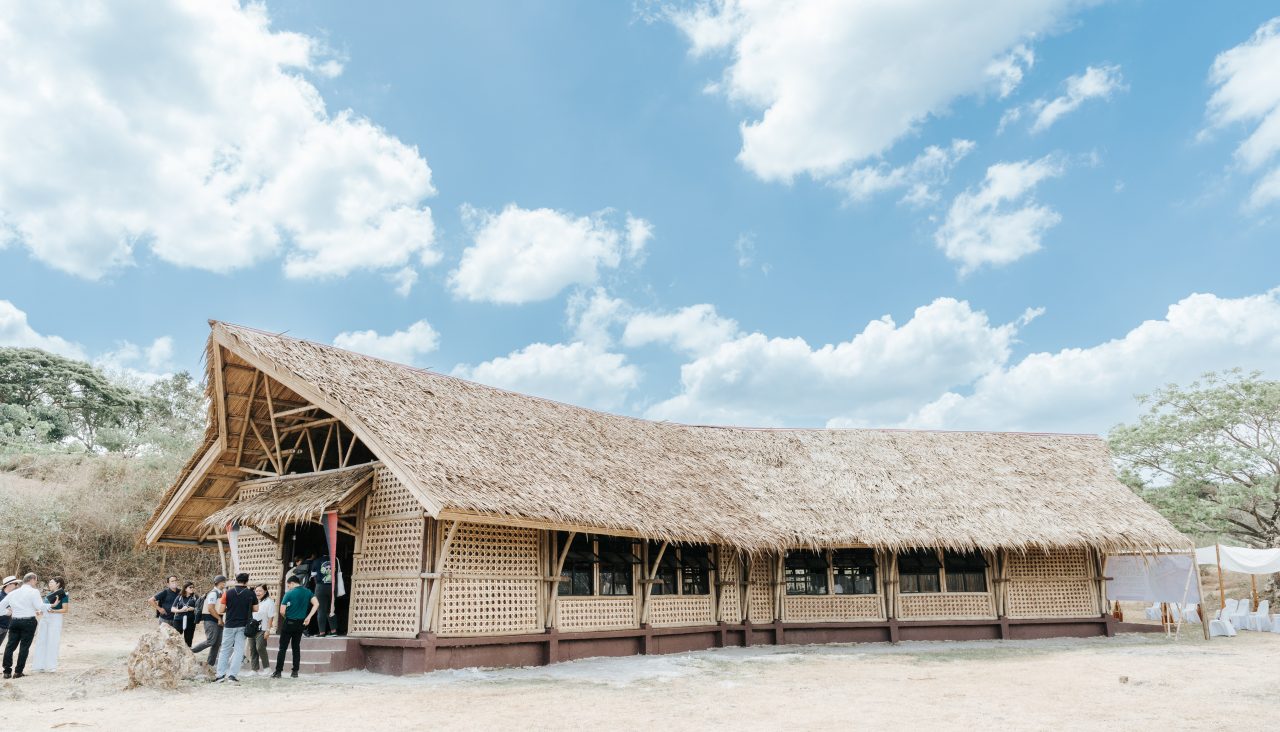
Tackling the Global Housing Crisis With Bamboo
Produced by the Hilti Foundation | September 13, 2023
By 2030, it is predicted that 3 billion people worldwide will be living in substandard housing. Affecting their education, health and livelihood, this is one of the reasons why underprivileged families remain in the so-called poverty trap.
To help alleviate this situation, the Hilti Foundation, together with the BASE Bahay Foundation, collaborate for affordable technology solutions to improve housing and the lives of low-income families. Having already set up a strong position in driving bamboo as a building material for low-cost housing, both organizations see this as a way to help mitigate the global housing crisis with a green and sustainable solution.
Green, disaster-resilient and local
To utilize existing building materials and promote the local economy, BASE introduced Cement Bamboo Frame Technology (CBFT), which was developed by the Hilti Foundation in 2012. This innovative construction technology uses treated, load-bearing bamboo as its sole structural element.
To date, more than 1,400 affordable homes for over 7,000 people in need have been built with CBFT. While the technology has been applied primarily in the Philippines and Nepal, the global housing crisis affects the entire Global South.
This indicates the need for safe, affordable and disaster-resilient homes for an estimated 1.6 billion people across the region by 2025. By supporting the development of various affordable housing solutions and technologies like CBFT, the Hilti Foundation helps to increase longevity of these people’s homes, preventing them from having to rebuild their homes after severe natural disasters and as they can build with higher quality. This enables a healthier and safer future for their families.
Bamboo construction benefits
BASE transforms into a leading hub in bamboo construction with a focus on low-income families. Amongst their CBFT is one solution which provides not only safety and reliability, but also boosts the local economy among the many benefits.
Bamboo keeps buildings naturally cool, and its flexibility allows them to withstand earthquakes of magnitude 7-8 and typhoons with winds of up to 300 km/h. The structures are extremely durable and resilient and have also been tested for their resistance to fire and insect infestation.
With an estimated lifetime of up to 60 years, the environmental impact of a CBFT house is 60% less than that of a conventional concrete house, according to a life cycle analysis by ETH Zurich. That correlates to a nine-ton reduction in carbon emissions during that time, making it even preferrable to wood in terms of environmental impact.
Another important fact is that bamboo is a renewable and cost-effective local resource in the Global South. According to Philippine Statistics Authority, the inflation rate for building materials in the Philippines has increased significantly since 2021, reaching 11% in October 2022. Since bamboo is locally abundant, it incurs no import or transportation expenses, and its supply chain contributes to local economies.
Driving a bamboo construction industry with Base
Since its inception, the BASE Bahay Foundation has been committed to developing independent bamboo treatment centers that supply high-quality engineered bamboo to its construction sites. Today, that commitment has shifted to creating a full-scale bamboo construction industry in the country, further enabling the local economy.
Independent entrepreneurs are supplying the housing market with treated bamboo, housing made from engineered bamboo such as doors, window frames or furniture, and even full-house solutions for low-income families with small but steady incomes.
In 2021, the foundation opened its BASE Innovation Center, a fully equipped testing facility that serves as a research and training center for bamboo construction. It enables public, private and third-sector partners to leverage technology for low-cost construction at an industrial scale.
The Base Innovation Center collaborates with more than 25 leading international and local universities, including ETH Zurich, Coventry University, the University of the Philippines and Virginia Tech, as well as corporate research partners like Hilti, Arup or Holcim.
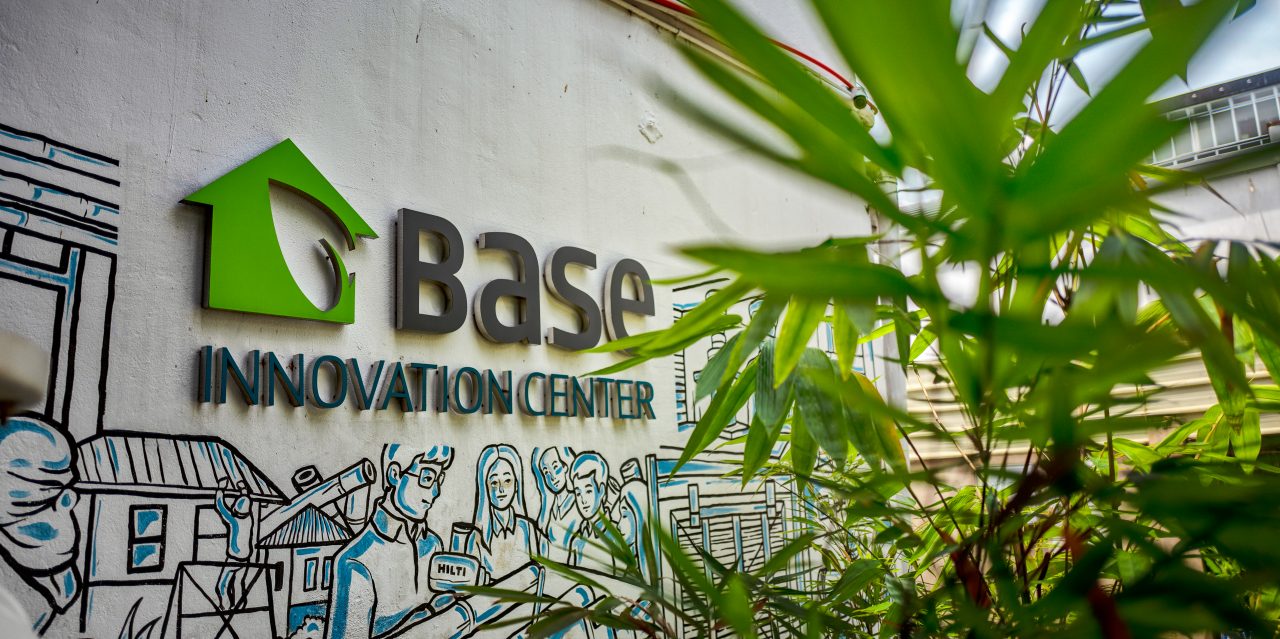
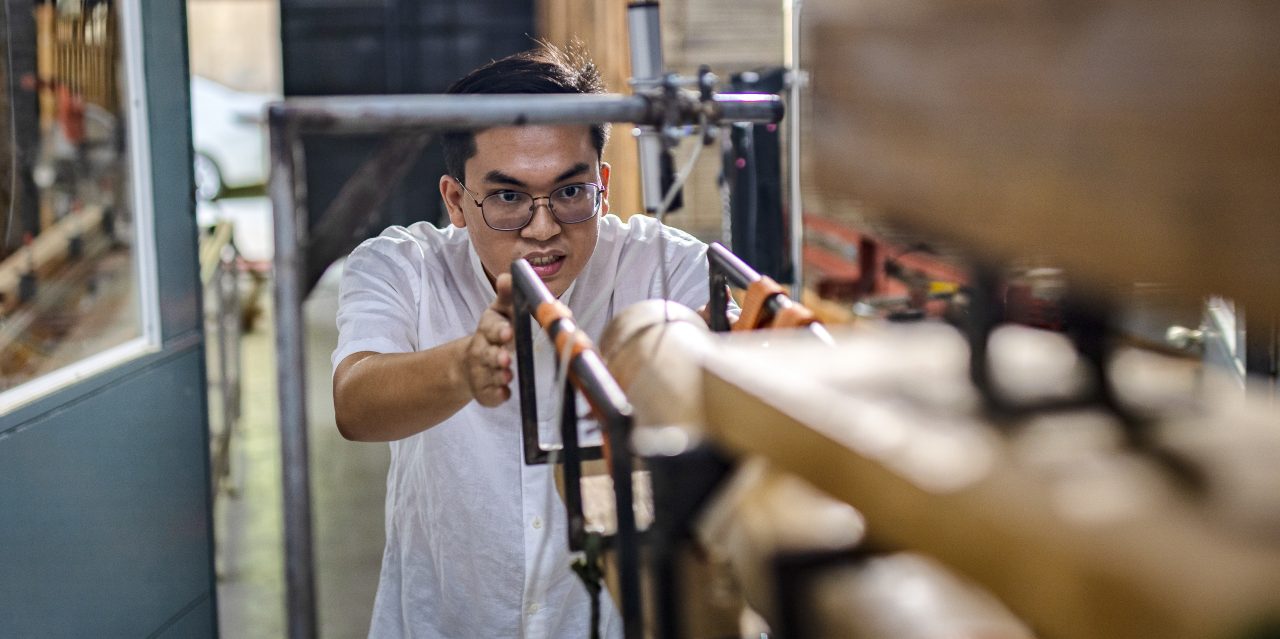
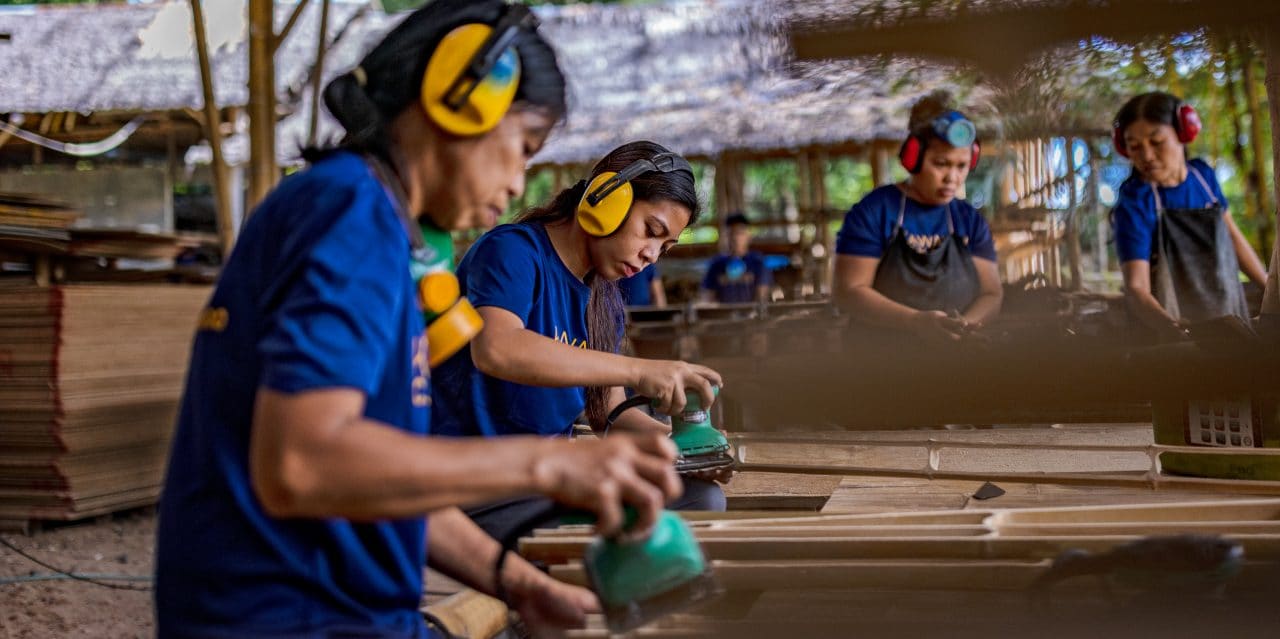
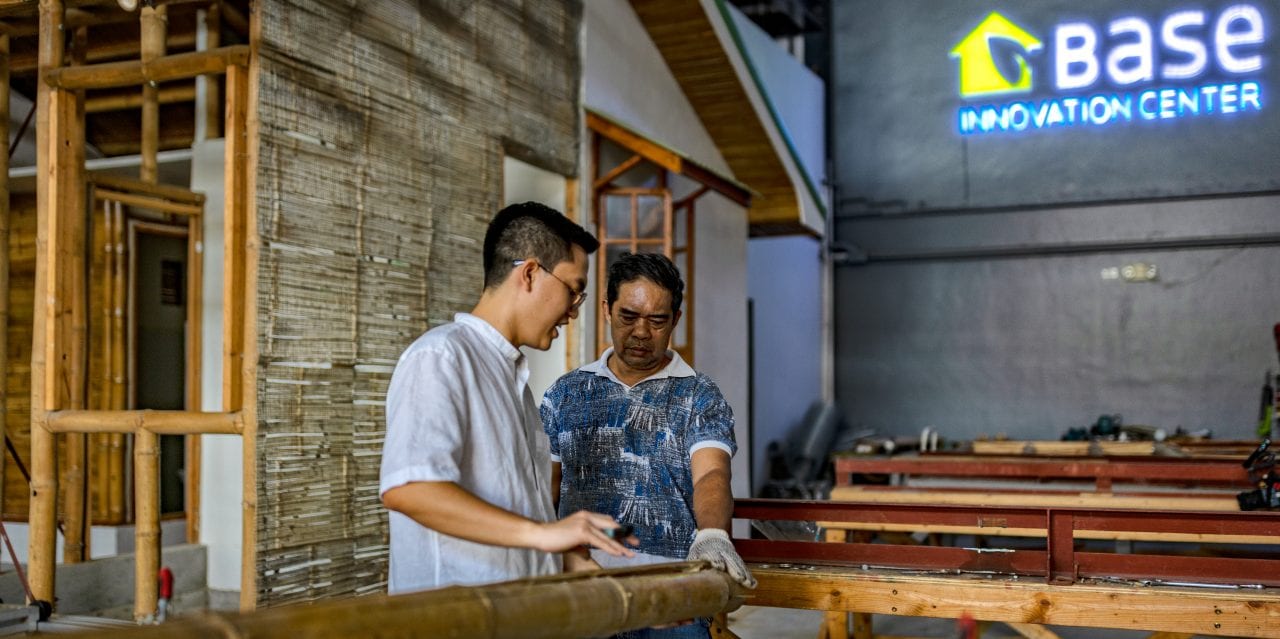
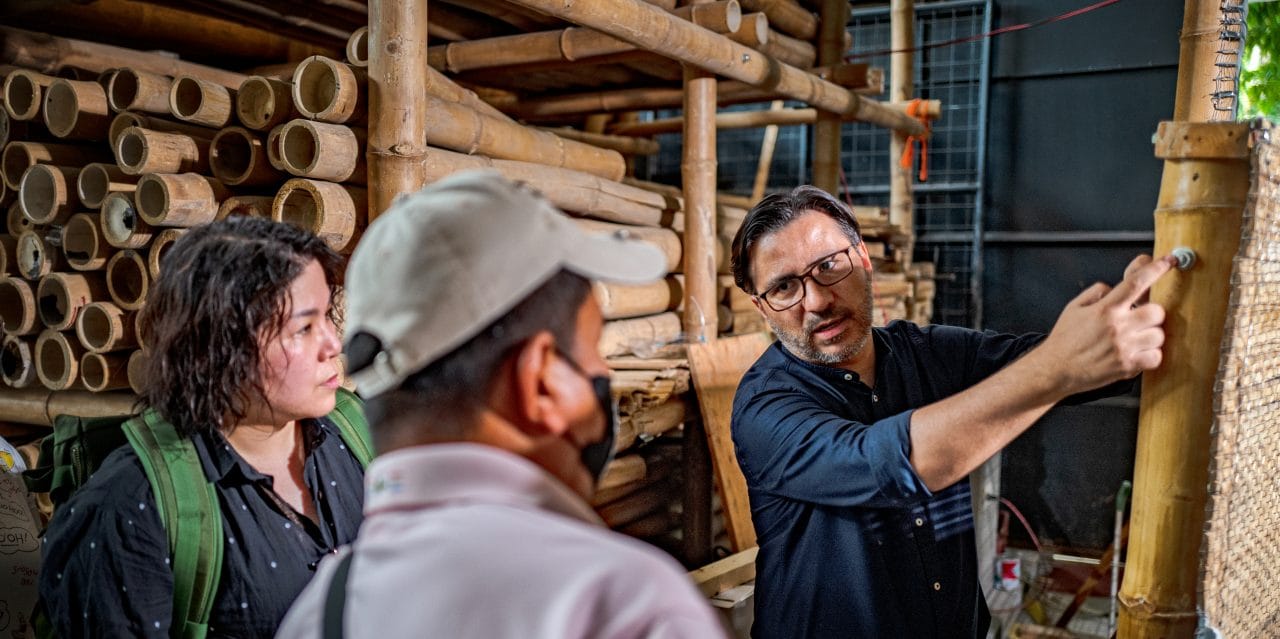
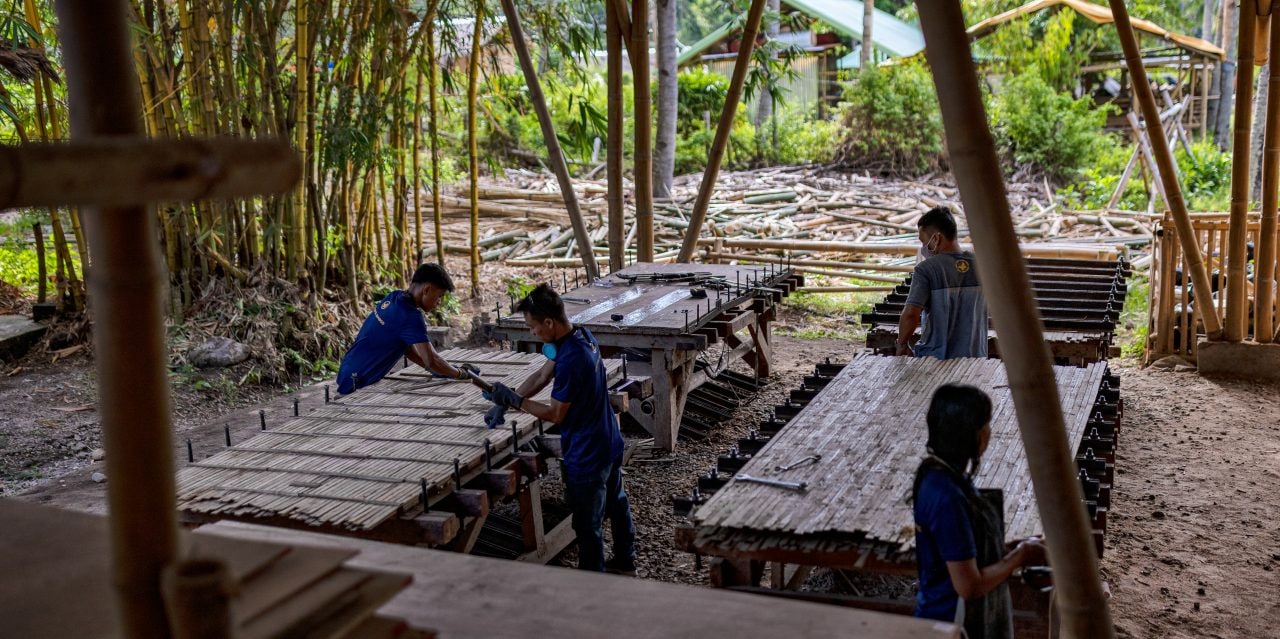
Bamboo Academy: Sharing knowledge internationally
Additionally, the BASE Bamboo Academy provides government-approved training for developers, architects, engineers, masons and others. They learn how to use bamboo as a building material, applying standards and norms developed for the national building codes.
Training is also offered to international partners who build with bamboo, helping more people in the Global South have green and safe homes. Just like 34-year-old Desiree from Manila: “I am happy with our new home. Here, I am no longer afraid that the roof will be blown away by strong winds. Now, my kids have a safe place to live.”
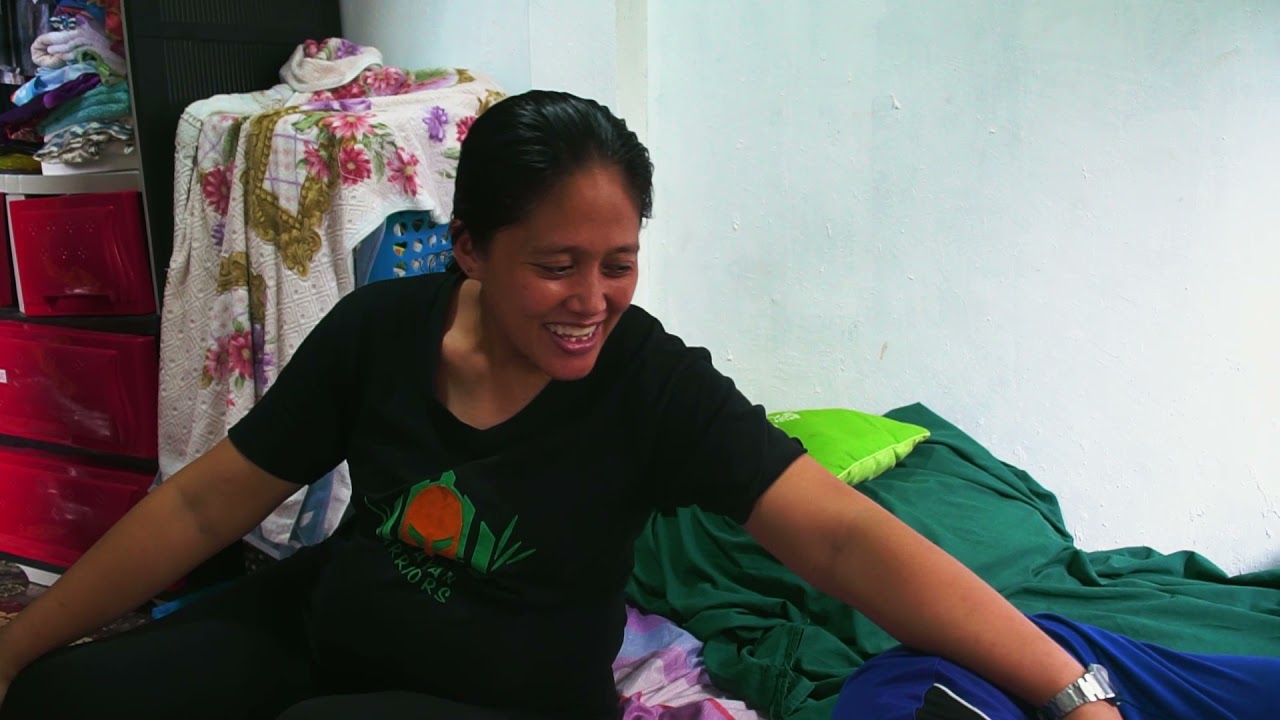
Generating impact with green building technology
From the outset, CBFT has been further developed at BASE Bahay’s Innovation Center together with renowned international universities. It also showed great potential to be used in larger buildings to provide livelihood opportunities for families from disadvantaged backgrounds and their communities.
Together with the BASE Bahay Foundation and other local partners, the Hilti Foundation has introduced bamboo as a building material for large community structures such as food processing facilities, schools or market halls, and recently inaugurated a weaving center in the Philippines.
“It's great to see how successfully our cement-bamboo frame technology is being utilized for large structures. Especially in the current situation, using bamboo as a local building material helps mitigate the impact of inflation on construction costs. This makes it an ideal material for communities looking for affordable and sustainable building options with durable structures that will stand the test of time. We believe this approach not only creates economic opportunities for local communities but also contributes to the region's overall resilience in the face of economic challenges,” says Werner Wallner, CEO of the Hilti Foundation.
To make bamboo a preferred building material in the developing world, both the Hilti Foundation and BASE Bahay Foundation continue to build networks and partnerships around the world. Through research, construction and finance, they keep focusing on the housing needs of low-income families.
High-tech bamboo technology
For over 5,000 years, bamboo has been used as a cheap and accessible construction material in many countries of the Global South. However, pure bamboo structures are not durable enough to withstand the frequent disasters in the region, such as typhoons and earthquakes. But Hilti Foundation's green and disaster resilient Cement Bamboo Frame Technology (CBFT) has transformed bamboo from a low-tech raw material into a high-tech building resource for safe and sustainable construction.
Disaster-resilient construction
Inspired by ancient Latin American building techniques, CBFT combines Asian bamboo construction traditions with the highest European standards in timber construction. The unique, prefabricated and sustainable frame system of treated load-bearing bamboo with metal connections and mortar-cement plaster enables the construction of stronger homes in less time. The technology has been tested for resistance to earthquakes of magnitude 7-8 and typhoons having winds of up to 300 km/h.
Green, local and affordable
CBFT has also been tested for resistance to fire and insect infestation, and structures with CBFT exhibit significant durability and resilience. With an estimated lifetime of 60 years, the environmental impact of a CBFT house is 60% less than a conventional concrete house, according to a life cycle analysis by ETH Zurich. This correlates to a reduction in carbon emissions of nine tons during that time. Another significant benefit is that bamboo is a highly renewable and cost-effective local resource. It is extremely sustainable and 25 to 50% less expensive compared to conventional buildings of the same quality, depending on the structure.